As we’ve discussed in Corrosion Under Insulation: The 7 Inspection Methods You Must Know About, pulsed eddy currents (PEC) is one of the tools at the industry’s disposal to find and monitor corrosion under insulation (CUI) because it’s capable of measuring a component’s wall thickness through its insulation, in real-time.
Generally, inspection service companies and asset owners are called to use PEC to find CUI on carbon steel pipes over non-conductive insulation such as mineral wool, wrapped in a metal weather jacket (also referred to as cladding). Worldwide, the most common type of weather jacket material is non-ferromagnetic aluminum, but in some regions ferromagnetic galvanized steel is dominant and it has proven to be an enormous challenge for pulsed eddy currents. Here’s why.
Galvanized Steel Attenuates PEC Signals
Pulsed eddy currents work by emitting an electromagnetic signal through the insulation towards the component under test, and then listening to the signal that comes back. A layer of conductive galvanized steel between the probe and the target component attenuates the PEC signal (much more so than aluminum). Excessive attenuation reduces the signal-to-noise ratio (SNR) below acceptable levels, making inspection results unreliable. As you can see from the following figure, the galvanized steel strongly attenuates the signal that reaches the inspected component.
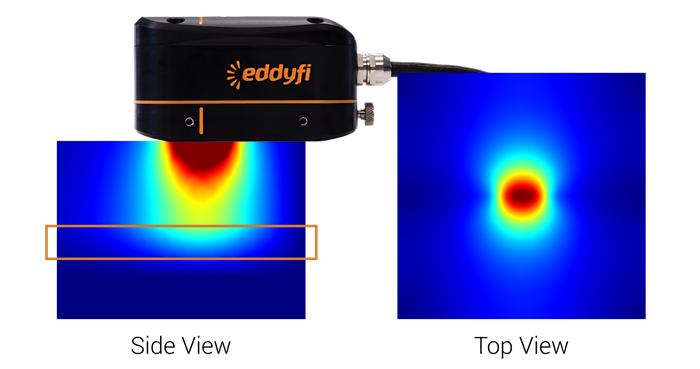
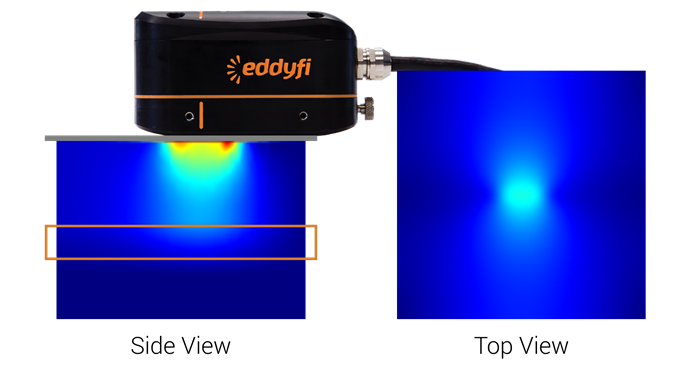
As you know, when placing a PEC probe on insulation, the emitted electromagnetic field spreads outward in a cone-like manner. The greater the liftoff (i.e., insulation), the larger the probe’s averaging area on the component becomes. Pulsed eddy current works by giving the average thickness of the entire averaging area. Therefore, if a defect under the probe is smaller the averaging area, the defect is under sized—it’s evaluated as smaller than it actually is.
Galvanized steel jacketing redirects the magnetic field in such a way that the electromagnetic cone becomes wider, resulting in a larger averaging area, which leads to greater under sizing of small defects, as illustrated here.
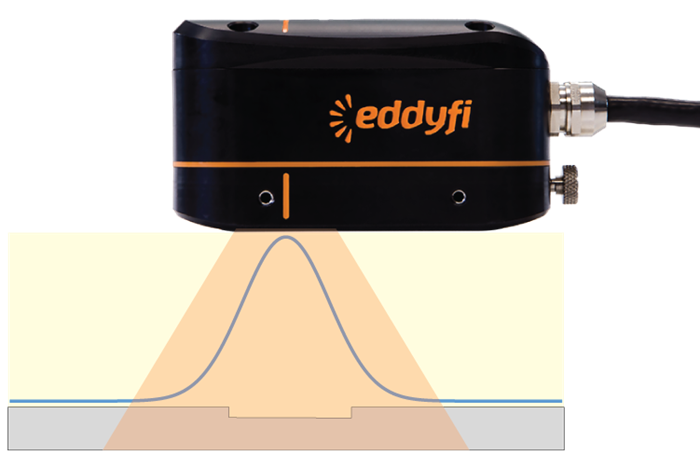
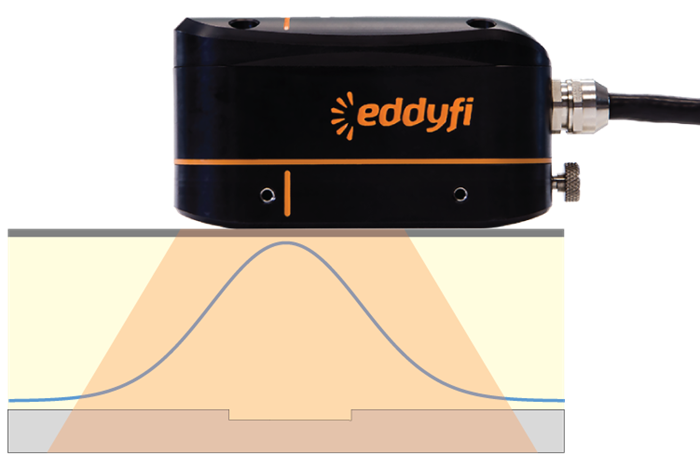
Each time the PEC probe emits a pulse, the ferromagnetic galvanized steel jacket vibrates from magnetostriction. At a PEC pulsation rate of 1–100 Hz, the strong vibration disrupts the PEC signal (as illustrated here).
The black line shows the signal amplitude variation in time during the analysis window. This effect makes the noise component of the SNR greater, lowering the ratio, which may lead to inadequate inspection results.
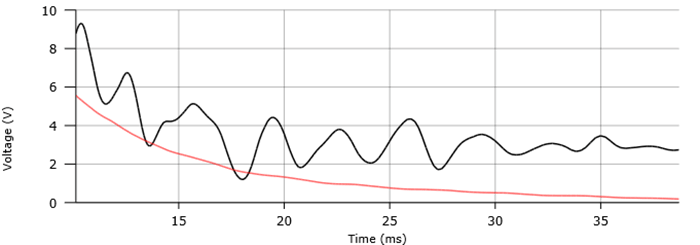
A few easy fixes exist to help mitigate these problems and make pulsed eddy current a truly reliable technique on all types of weather jackets. The first is to compensate for the attenuation effect with a larger probe and/or using a longer averaging time. This significantly increases the SNR and improves inspection results. Selecting the right probe for an inspection job is key. We supply a probe selection table relating liftoff and nominal wall thickness.
However, this table doesn’t take galvanized steel jacketing into account. A good rule of thumb for probe selection is a 0.5 mm (0.020 in) thick galvanized steel jacketing is roughly equivalent to adding 40 mm (~1.5 in) of liftoff between the probe and the component under test.
Accounting for the larger averaging area when reporting on defects in the presence of galvanized steel improves the accuracy of results. Here, the same rule of thumb applies to the averaging area and smallest detectable defects: 0.5 mm (0.020 in) thick galvanized steel jacketing is roughly equivalent to adding 40 mm (~1.5 in) of liftoff.
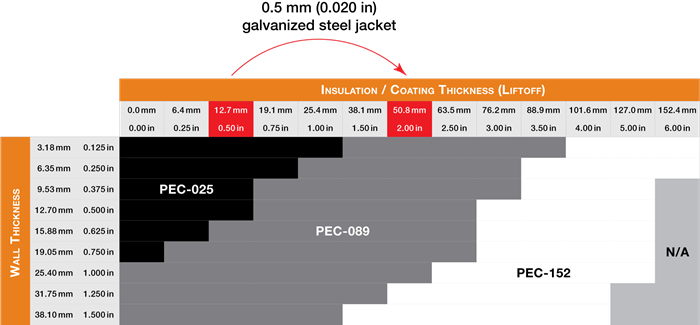
Finally, maximizing the mechanical coupling between the probe and the galvanized steel cladding dampens vibrations. This effectively lowers the “noise” component of the signal-to-noise ratio, improving inspection results. Outfitting a probe with a shoe specifically designed to dampen vibration has been shown to significantly improve the signal quality when working on galvanized steel. The following figure compares A-scan and C-scan data in three situations. The widening effect of the galvanized steel can be observed with the slightly undersized measured wall thickness and larger defect area. The measurement made with the vibration-dampening shoe is much less noisy and overall more accurate than the acquisition made without the shoe.

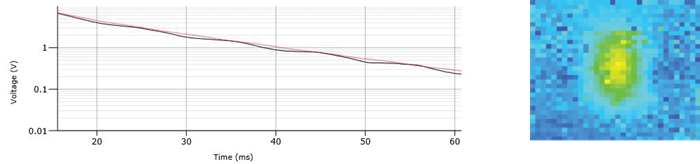
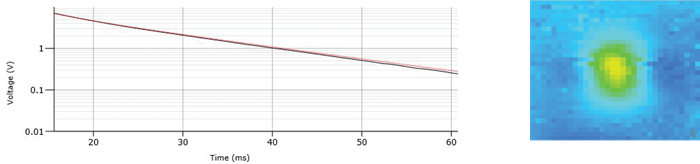
The lack of adoption of the PEC technique in some parts of the world is due in great part to the suboptimal performances of PEC tools in the presence of galvanized steel. To improve results, using a longer averaging time and taking the larger averaging area into account are paramount. It’s also very useful to remember the rule of thumb that a 0.5 mm (0.020 in) galvanized steel jacket roughly equals adding 40 mm (~1.5 in) of liftoff. This may mean selecting a different probe and expecting a different averaging area. Finally, using a vibration-dampening shoe vastly improves pulsed eddy current inspection results in the presence of a galvanized steel weather jacket.
Interested in continuing the conversation with one of our NDT experts? Complete the form below to get in touch and stay Beyond Current on relevant information related to inspecting galvanized steel and more!